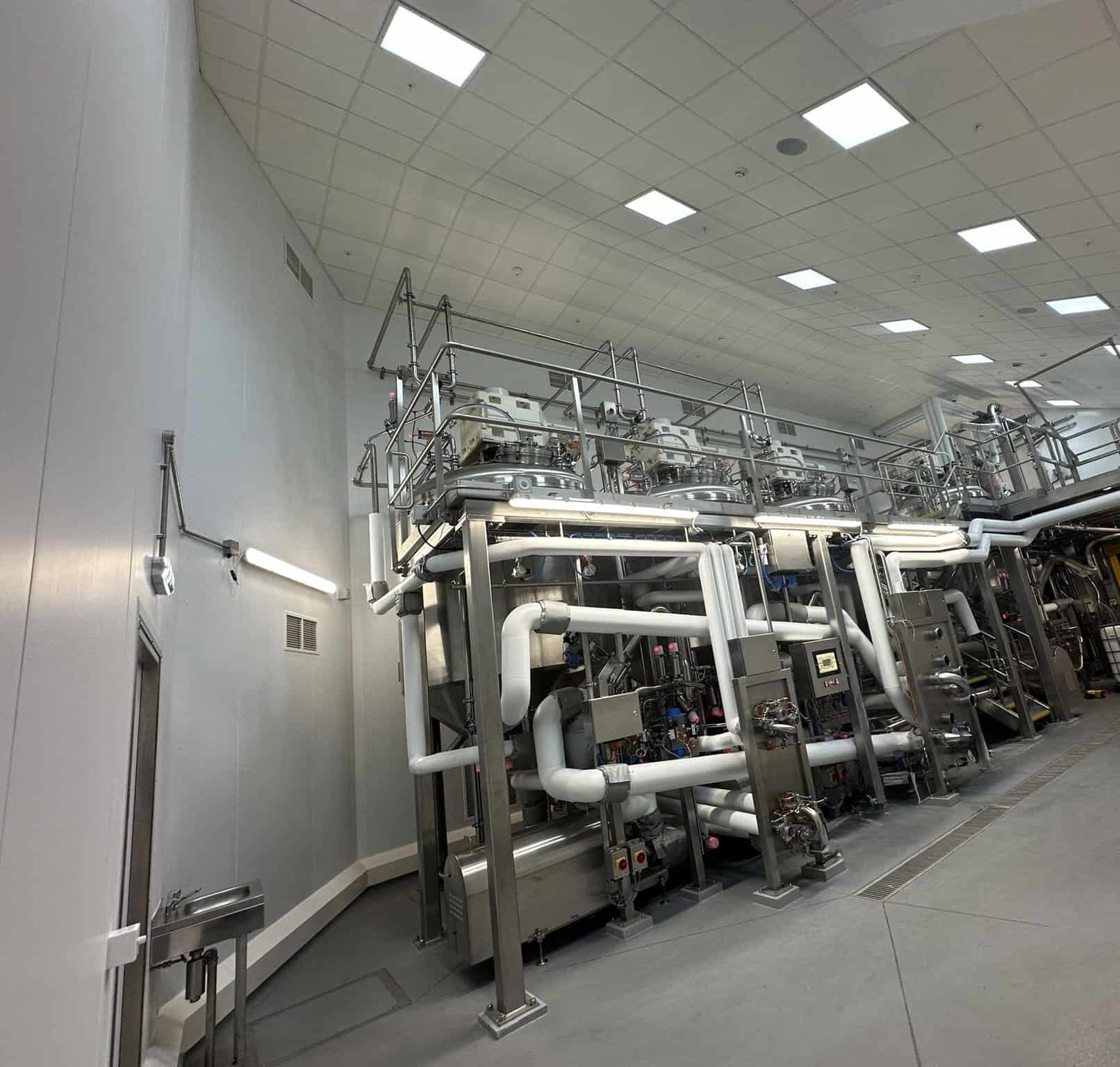
Challenge
This projects aim to provide a top tier pharmaceutical grade class 8 cleanroom facility within a live manufacturing area was the challenge put to our team. Working with our long term client and their process engineering supplier, Picow were appointed principle contractor and were tasked to provide a full turnkey service with all construction, mechanical and electrical works including associated designs. Agreeing final layouts and the order of the work to build this facility proved difficult as we were mindful that the best design would be one that impacted existing operations the least.
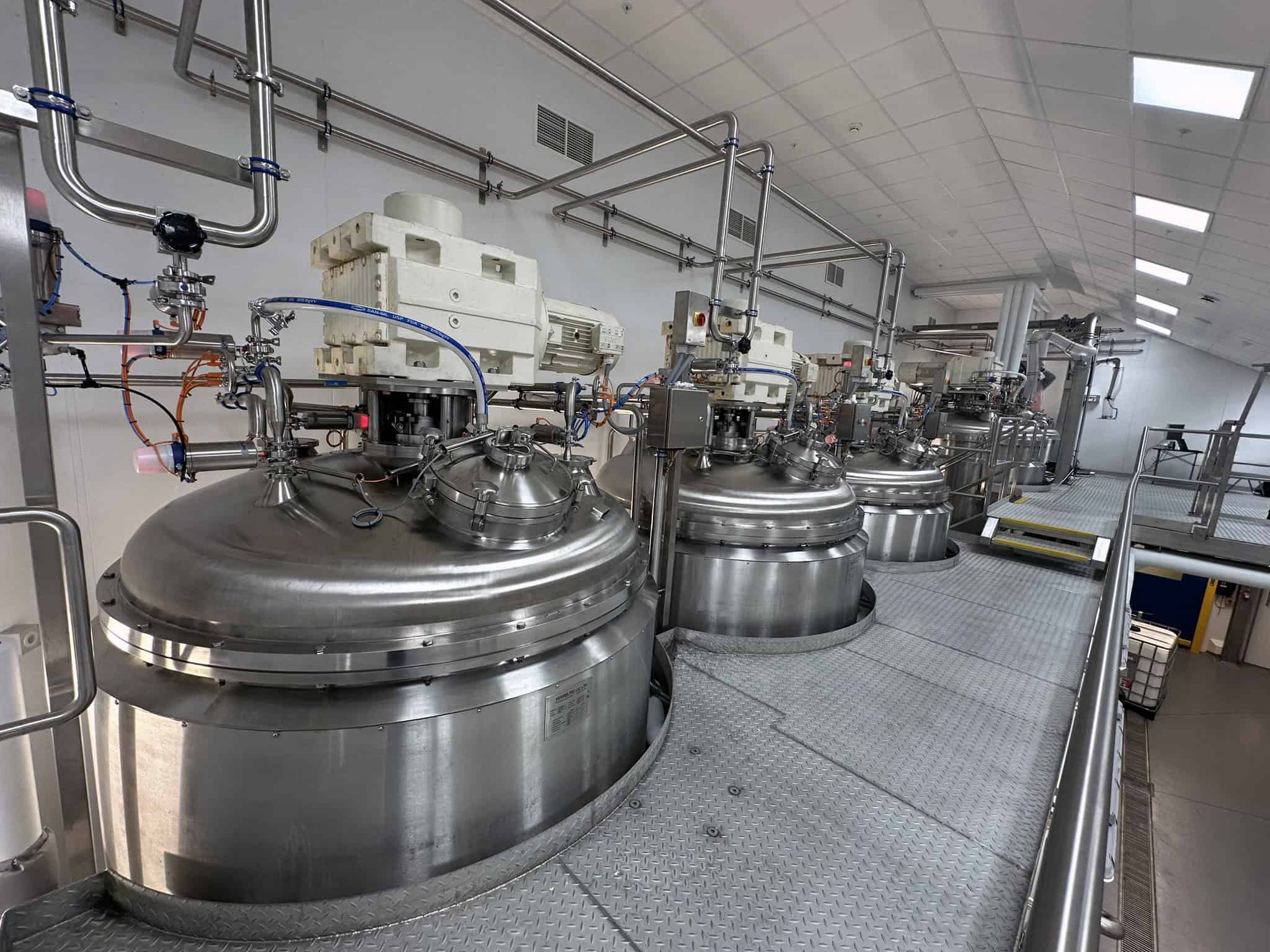
Solution
The project encompassed a wide range of activities, the first being the setup of a comprehensive compound and site boundary to ensure total segregation from existing site operations. We were then tasked with a round of enabling works involving underground drainage and internal mechanical and electrical services diversions. Construction works consisted of initially building an extension to provide the additional space needed. Internal piling and concrete works was also completed to ensure structural integrity with the added weight of the new tanks. The floor was finished with Stonclad UR heavy-duty polyurethane mortar. Kingspan Quadcore composite wall panels with a cleansafe120 finish were installed throughout. To maintain cleanliness, Polysto Sanicoat prefabricated polymer composite kerbs were installed on all new and existing walls. For the ceiling an Ecophon Hygiene Protec ‘A’ suspended system was utilised.
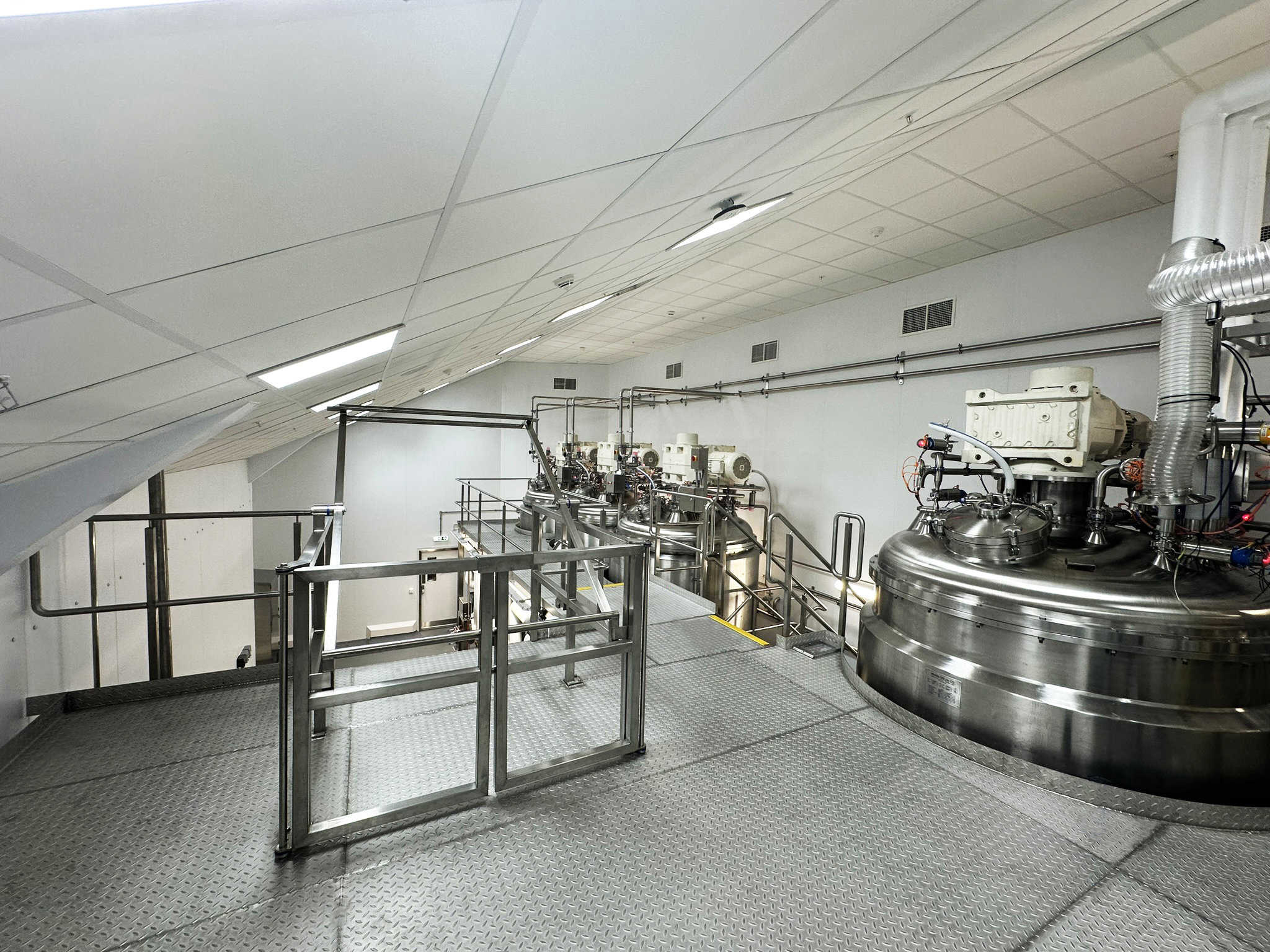
Solution
The comprehensive nature of the project extended to crucial elements such as the HVAC system to ensure a cleanroom 8 classification was achieved. In addition to this we installed stainless steel process pipework, sprinkler systems and associated mechanical controls. For the electrical installation we installed a number of main power cables from the sub station feeding the process MCC, local sub section board and distribution boards. Stainless steel cable management was installed throughout catering for small power, lighting, fire alarm and PA systems.
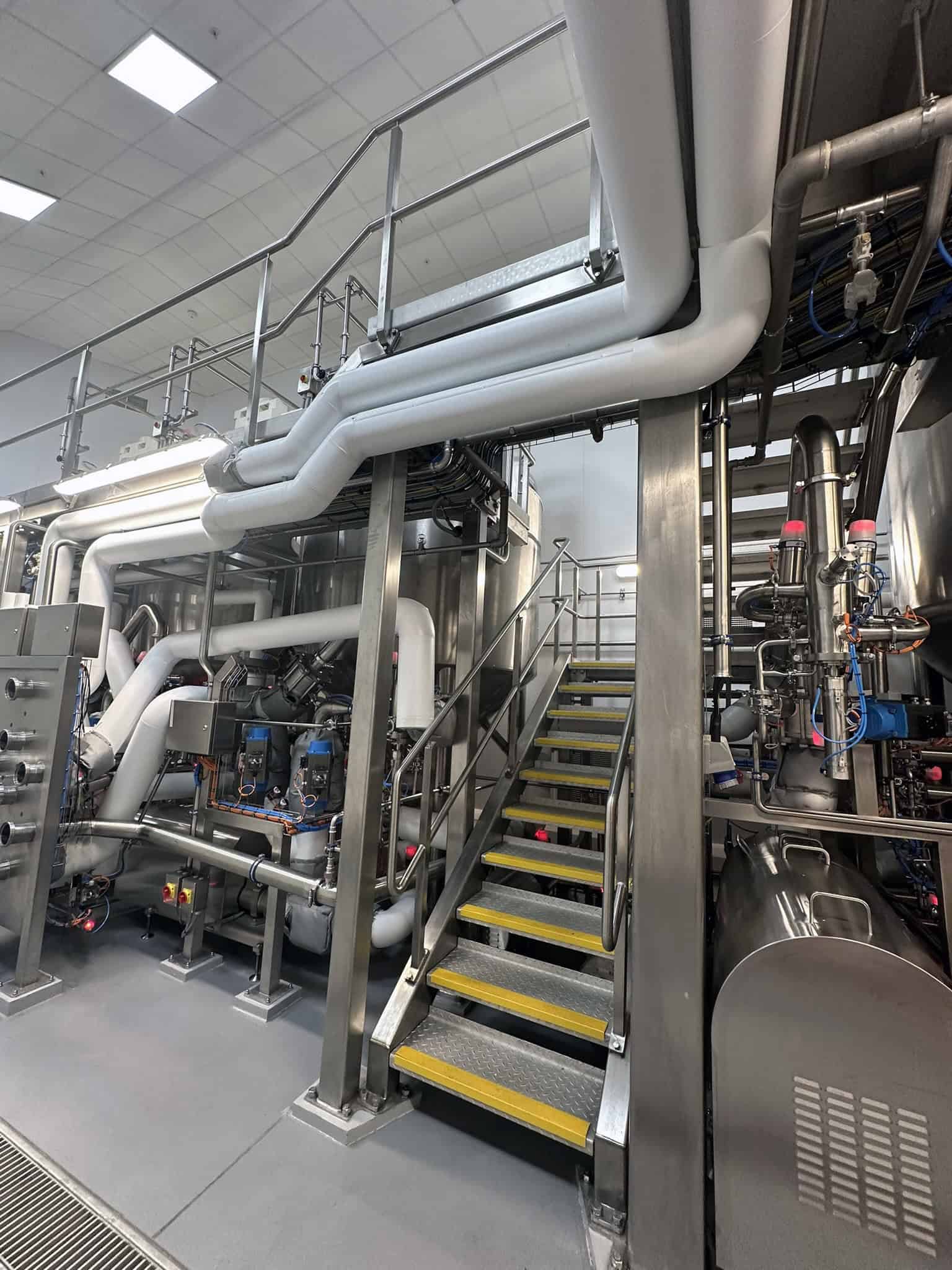
Outcome
Due to the constraints of working within a live pharmaceutical process facility, the success of the project lay in the up front planning and co-ordination at design and pre start stages. The sequencing of key phases of the project passed as planned and within the required timescales which was critical to achieving our clients planned manufacturing dates. A particular part of the project where the site team remained flexible throughout was with the work that needed to be completed out of hours when carrying out the piling and groundworks, with the associated noise and vibration affecting existing process operations. The finished cleanroom was an outstanding example of professional construction, combining all of our service expertise within one turnkey package.